Physical
limitations of water based coolants
Chemical
limitations of water based coolants
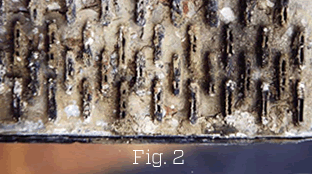
|
A
review of water based engine coolants
The Economax Engine Cooling System represents
a major step forward in engine cooling technology. To fully appreciate
the radical improvements facilitated by Economax, it is useful
to review current cooling technology.
Over the last 100 years engine design and
efficiency has improved significantly. In stark contrast engine
coolants have remained mostly unchanged since the 1930’s and
are still based on a mixture of Ethylene Glycol (EG), water
and corrosion inhibitors. All such mixtures have inherent physical
and chemical limitations that restrict engine performance and
effect reliability.
Physical limitations of water based
coolants
Within an engine cooling system the hottest surfaces are those adjacent to the
combustion chamber, specifically the cylinder liners and cylinder head. Evans
have proven that in these areas EG-Water mixtures regularly cross the thermal
boundary that separates efficient Nucleate Boiling (B in Fig.1) from inefficient
Critical Heat Flux.
CHF is synonymous with
the condition ‘Departure from Nucleate Boiling’ or DNB. When
DNB occurs in an engine cooling system a layer of steam bubbles
form adjacent to the engine hot-spots (A in Fig.1). Because
steam dissipates less than 1/30th of the heat that water does,
local metal temperatures over-heat rapidly.
This over-heating
leads to several problems including; thermal distortion of
the cylinder head and liners, pre-ignition (aka engine knock),
liner pitting, boil-over and after-boil. Over-heating is the
most common cause of engine down-time and responsible for >50% of catastrophic engine failures. |
Chemical
limitations of water based coolants
Although water is cheap and readily available, it is also the root cause of corrosion
within engine cooling systems (see Fig.2). Hence the necessity to add corrosion
inhibitors. Corrosion inhibitor formulations have changed many times over the
years, but not always for the better.
Nitrite, silicate, borate
and azole based products have been around for many years, with
Organic Acid Technology (OAT) inhibitors appearing more recently.
OAT formulations are often branded as ‘Long-Life’ based on
their five year life-span, compared with 1-2 years for standard
antifreeze formulations.
Although OAT-EG-Water
mixtures are now used in most new car engines, they have proven
less successful in Heavy Duty Diesel Engine (HDDE) cooling
systems. After several years of trying OAT based products many
OEMs and fleet operators reverted to nitrite and/or Hybrid
OAT (HOAT) formulations. One reason for this u-turn was that
OAT formulations offer little protection against liner pitting
- a major problem in HDDE.
To maintain effective
inhibitor levels it is often necessary to retro-dose with Supplemental
Coolant Additives or SCAs. It is common for SCA’s to be under
or over dosed leading to accelerated corrosion rates, cylinder
liner pitting or blocking up of radiator channels with congealed
inhibitor.
|